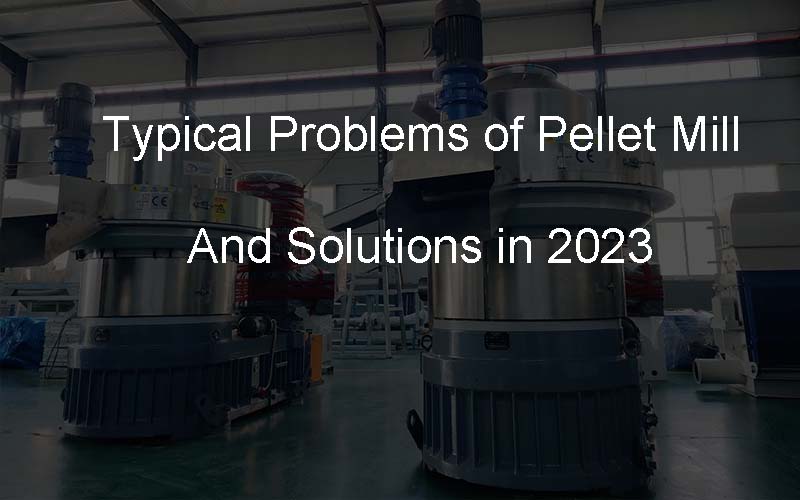
Maszyna do mielenia pelletu: typowe problemy i rozwiązania w 2023 r
Korzystanie z młynów do pelletu wiąże się z wieloma wyzwaniami. Użytkownicy młynów do pelletu staną w obliczu szeregu typowych problemów, które mogą utrudniać ich procesy produkcyjne.
Niestała jakość pelletu, emisja pyłu, wysokie zużycie energii i awarie sprzętu wpływają na wydajność, produktywność i ogólną rentowność.
W tym artykule przyjrzymy się najczęstszym problemom napotykanym w pelletowniach i przedstawimy praktyczne rozwiązania ich rozwiązania.
Przyjmując odpowiednie praktyki konserwacji, optymalizując parametry operacyjne i wdrażając skuteczne strategie, operatorzy mogą pokonać te wyzwania i zwiększyć produkcję pelletu.
Przedstawiamy TCPEL, wiodącego Młyn do pelletu B2B firmy i jej rozwiązań, które pomogą użytkownikom przezwyciężyć te problemy. Przyjrzyjmy się więc typowym problemom pelletowni w 2023 roku i znajdźmy możliwe rozwiązania, aby je pokonać.
Jak działa młyn do pelletu
Przed zagłębieniem się w specyficzne problemy młynów do pelletu, ważne jest zrozumienie działania młyna do pelletu.
Młyny do pelletu mogą przekształcać surowce w pelety. W tym pelety drzewne, pelety z biomasy. Pellety te można wykorzystać do różnych celów. Takie jak paliwo, pasza dla zwierząt.
Surowce będą granulowane za pomocą maszyn do peletowania na cylindryczne peletki. Istnieje szereg procesów, podgrzewanie, nawilżanie i obróbka.
Młynki do peletowania składają się z kilku elementów, w tym podajnika, kondycjonera, matrycy do peletowania, rolek i silnika. Podajnik zapewnia stały dopływ surowców do maszyny, podczas gdy kondycjoner dodaje wilgoć i ciepło, aby wspomóc proces peletyzacji.
Matryca i rolki peletu wywierają nacisk i ściskają materiały, kształtując je w peletki o pożądanej wielkości i gęstości. Silnik zapewnia moc niezbędną do napędzania działania maszyny[1].
Jeśli chcesz znaleźć najlepszy sposób rozwiązania problemów podczas przetwarzania, dowiedz się więcej o podstawach młyna do pelletu.
Mając dogłębną wiedzę na temat działania maszyny i jej kluczowych komponentów, operatorzy mogą lepiej rozwiązywać problemy i wdrażać skuteczne rozwiązania.
W kolejnych sekcjach przyjrzymy się typowym problemom, z jakimi borykają się granulatory w 2023 r., i przedstawimy praktyczne rozwiązania umożliwiające ich przezwyciężenie.
Młyny do pelletu paszowego: Jakość pelletu niespójna
Jednym z częstych problemów napotykanych podczas korzystania z młynka do peletek jest niespójna jakość peletu. Pelety mogą różnić się rozmiarem, gęstością i trwałością, co może wpływać na ich wydajność i wartość rynkową.
Niespójna jakość peletu może prowadzić do niezadowolenia klientów i zmniejszenia rentowności.
Rozwiązanie
Aby rozwiązać ten problem, należy zapewnić odpowiednią obróbkę i kondycjonowanie surowców przed wejściem do komory peletyzującej.
Kontrolowanie zawartości wilgoci, wielkości cząstek i temperatury materiału może znacznie poprawić jakość peletu. Właściwe kondycjonowanie pomaga zmiękczyć surowiec, ułatwiając formowanie go w pelety[2].
Ponadto stosowanie wysokiej jakości matryc do młynów do peletowania oraz regularna ich kontrola i konserwacja mogą przyczynić się do utrzymania stałej jakości peletu.
Młyny do pelletu drzewnego: Zablokowanie matrycy do pelletu
Kolejnym wyzwaniem, przed którym stoją operatorzy peletek, jest zablokowanie lub zatkanie matrycy peletu. Może to nastąpić z powodu takich czynników, jak wysoka zawartość wilgoci, nadmierne nagromadzenie materiału lub przedostanie się ciał obcych do matrycy.
Zablokowanie matrycy zakłóca proces produkcji peletu i wymaga częstych wyłączeń maszyny w celu jej oczyszczenia.
Rozwiązanie
Aby zapobiec zatorom, ważne jest monitorowanie i utrzymywanie odpowiedniej wilgotności surowców. Nadmierna wilgoć może spowodować sklejanie się materiału i zatykanie matrycy [3].
Regularne sprawdzanie matrycy pod kątem jakichkolwiek oznak zatkania lub uszkodzenia oraz dokładne jej czyszczenie może pomóc w uniknięciu przerw w produkcji.
Ponadto wdrożenie odpowiednich technik podawania, takich jak stosowanie jednolitych i stałych prędkości podawania oraz stosowanie odpowiednich dodatków, może przyczynić się do płynniejszej pracy i zmniejszenia ryzyka zablokowania matrycy.
Maszyna do mielenia pelletu: Niskie wskaźniki produkcji pelletu
Młyny do peletowania często napotykają problemy związane z niskimi wskaźnikami produkcji peletu. Czynniki takie jak nieefektywna kompresja, nieodpowiednia grubość matrycy lub zużyte części mogą przyczynić się do obniżenia wydajności.
Niskie tempo produkcji może utrudniać sprostanie wymaganiom klientów i ograniczać generowanie przychodów.
Rozwiązanie
Aby zwiększyć produkcję pelletu, kluczowa jest optymalizacja procesu prasowania poprzez dostosowanie parametrów granulatora, takich jak grubość matrycy, nacisk rolek i temperatura kondycjonowania.
Grubość matrycy powinna być odpowiednia dla przetwarzanego surowca, aby zapewnić odpowiednią kompresję i formowanie peletu [4].
Regularna kontrola i wymiana zużytych części, takich jak rolki i matryce, jest również ważna dla utrzymania optymalnej wydajności.
Ponadto upewnienie się, że granulator jest odpowiednio nasmarowany i wyrównany, może przyczynić się do poprawy wydajności produkcji.
Producenci młynów do pelletu: Emisja pyłu
Emisja pyłu jest istotnym i powszechnym problemem, z którym operatorzy muszą się uporać podczas obsługi granulatorów. Obecność nadmiernego zapylenia w zakładzie produkcyjnym może stwarzać szereg problemów o poważnych konsekwencjach.
Po pierwsze, stwarza zagrożenie dla zdrowia operatorów, którzy na co dzień są narażeni na działanie cząstek unoszących się w powietrzu. Wdychanie pyłu może prowadzić do problemów z oddychaniem i innych komplikacji zdrowotnych, zagrażając dobremu samopoczuciu siły roboczej.
Nagromadzenie kurzu może zakłócić prawidłowe działanie wyposażenia młyna do peletek. Gdy kurz osadza się na wrażliwych elementach, takich jak silniki, paski i układy sterowania, może powodować nieprawidłowe działanie, awarie i nieplanowane przestoje.
To nie tylko zakłóca proces produkcyjny, ale także skutkuje zwiększonymi kosztami konserwacji i zmniejszoną ogólną wydajnością.
Nadmiar pyłu może negatywnie wpływać na środowisko pracy, powodując dyskomfort dla operatorów. Zapylone powietrze może ograniczać widoczność, powodować dyskomfort i wpływać na ogólną czystość obiektu.
Ponadto, jeśli nie jest odpowiednio kontrolowana, emisje pyłu mogą prowadzić do niezgodności z normami regulacyjnymi i przepisami dotyczącymi ochrony środowiska, co może skutkować karami pieniężnymi.
Rozwiązanie
Aby ograniczyć emisję pyłu, niezbędne jest wdrożenie skutecznych systemów odpylania, takich jak cyklony czy filtry workowe. Systemy te wychwytują i zatrzymują pył powstający podczas procesu peletyzacji.
Regularne czyszczenie i konserwacja sprzętu, w tym granulatora i powiązanych systemów wentylacyjnych, może znacznie zmniejszyć poziom pyłu. Właściwe obchodzenie się i przechowywanie surowców może również pomóc zminimalizować powstawanie pyłu.
Stosowanie materiałów niskopyłowych lub wstępnie kondycjonowanych może dodatkowo zmniejszyć ilość wytwarzanego pyłu. Ważne jest, aby przeszkolić operatorów w zakresie odpowiednich procedur kontroli zapylenia i zapewnić im odpowiedni sprzęt ochrony osobistej, aby zapewnić bezpieczne środowisko pracy.
Producenci młynów do pelletu: Zużycie energii
Niektóre granulatory napotykają problemy związane z nadmiernym zużyciem energii. Może to prowadzić do wzrostu kosztów eksploatacji i zmniejszenia ogólnej wydajności maszyny.
Wysokie zużycie energii może obciążać zasilanie, zwiększać emisję dwutlenku węgla i wpływać na zrównoważony rozwój procesu produkcji pelletu.
Rozwiązanie
Aby sprostać wysokiemu zużyciu energii, kluczowa jest optymalizacja parametrów pracy pelletu. Dostosowanie czynników, takich jak prędkość walca, grubość matrycy i kondycjonowanie materiału, może pomóc w osiągnięciu lepszej efektywności energetycznej.
Znajdując właściwą równowagę między siłą kompresji a wkładem energii, operatorzy mogą zmaksymalizować produkcję pelletu przy jednoczesnym zminimalizowaniu zużycia energii. Regularna konserwacja, w tym smarowanie i osiowanie maszyny, jest również ważna dla zmniejszenia strat energii.
Modernizacja na bardziej energooszczędne komponenty i stosowanie zaawansowanych systemów sterowania może dodatkowo przyczynić się do oszczędności energii.
Maszyny do mielenia pelletu: Przeciążenie młyna do pelletu
Częstym problemem napotykanym przez operatorów granulatorów jest przeciążenie lub zakleszczanie się granulatora, które może wystąpić z powodu takich czynników, jak ciała obce, niewłaściwe podawanie materiału lub awaria sprzętu.
Przeciążenie lub zakleszczenie może spowodować przestoje, opóźnienia w produkcji i uszkodzenie elementów granulatora.
Rozwiązanie
Aby zapobiec przeciążeniu i zakleszczeniu, konieczne jest wdrożenie odpowiednich technik obsługi i podawania materiału. Operatorzy powinni upewnić się, że surowce są wolne od zanieczyszczeń, takich jak kamienie, metale lub duże cząstki, które mogą powodować zatory.
Regularna kontrola systemu żywienia i sprzętu, w tym podajnika i kondycjonera, jest konieczna, aby szybko zidentyfikować i rozwiązać wszelkie problemy. Wdrożenie środków bezpieczeństwa, takich jak wykrywacze metali lub separatory magnetyczne, może pomóc w zapobieganiu przedostawaniu się ciał obcych do granulatora.
Ponadto operatorzy powinni postępować zgodnie z wytycznymi producenta dotyczącymi obsługi granulatora w ramach jego określonej wydajności, aby uniknąć przeciążenia.
Matryca młyna do pelletu: Twardość peletu
Nierówna twardość peletu jest częstym problemem spotykanym w młynach do peletowania. Odnosi się to do zmian gęstości i twardości wytwarzanych peletów. Niespójna twardość może wpływać na jakość peletów i ich wydajność podczas spalania lub stosowania jako pasza dla zwierząt.
Rozwiązanie
Aby rozwiązać problem nierównej twardości pelletu, ważne jest zapewnienie odpowiedniego kondycjonowania i sprasowania surowców. Utrzymanie stałej zawartości wilgoci w całym procesie peletyzacji ma kluczowe znaczenie dla uzyskania jednolitej twardości peletu.
Dodatkowo regulacja nacisku rolki i grubości matrycy może pomóc w kontrolowaniu gęstości i twardości peletów. Regularna kontrola i konserwacja elementów młyna, takich jak rolki i matryce, jest również ważna dla zapewnienia stałej jakości peletu.
Maszyny do mielenia pelletu: Hałas w młynie do pelletu
Problemy z wibracjami i hałasem są często spotykane w młynach do peletowania, które mogą wpływać na środowisko pracy i potencjalnie uszkodzić sprzęt.
Nadmierne wibracje mogą prowadzić do przyspieszonego zużycia maszyny, a wysoki poziom hałasu może powodować dyskomfort i uszkodzenie słuchu u operatorów.
Rozwiązanie
Aby złagodzić problemy z wibracjami i hałasem, ważne jest, aby młynek do peletek był prawidłowo zainstalowany i wyrównany. Właściwe wyrównanie pomaga zminimalizować wibracje i zapewnia płynną pracę.
Regularne kontrole i konserwacja elementów maszyny, w tym łożysk i pasów, również mogą zmniejszyć poziom wibracji.
Wdrożenie środków dźwiękochłonnych, takich jak ogrodzenie młyna do peletu lub zastosowanie ekranów akustycznych, może pomóc w ograniczeniu emisji hałasu. Smarowanie ruchomych części, takich jak łożyska, również może przyczynić się do płynniejszej pracy i zmniejszenia poziomu hałasu[5].
Rozwiązując problemy związane z nierównomierną twardością peletów oraz wibracjami/hałasem, operatorzy mogą zwiększyć ogólną wydajność i wydajność swoich młynów do peletek, co prowadzi do poprawy jakości peletów i lepszego środowiska pracy.
Matryca młyna do pelletu: Zablokowanie z powodu materiałów o wysokiej zawartości włókien
Podczas korzystania z materiałów o wysokiej zawartości włókien, takich jak niektóre rodzaje pozostałości rolniczych lub biomasy, granulatory mogą napotkać problemy z zablokowaniem matrycy. Wysoka zawartość błonnika może prowadzić do powstawania uporczywych zatorów w matrycy peletu, utrudniając proces produkcji peletu.
Rozwiązanie
Aby przezwyciężyć blokadę matrycy spowodowaną przez materiały o wysokiej zawartości włókien, ważne jest wdrożenie skutecznych technik przygotowania materiału. Wstępne przetwarzanie surowców, takie jak mielenie lub rozdrabnianie, może pomóc w zmniejszeniu długości włókien i ułatwić płynniejszą produkcję pelletu.
Dodatkowo, dostosowanie zawartości wilgoci i użycie odpowiednich spoiw lub dodatków może poprawić płynność materiałów i zapobiec zatykaniu matrycy. Regularna kontrola i czyszczenie matrycy peletu jest również kluczowe dla utrzymania nieprzerwanej produkcji peletu.
Maszyny do mielenia pelletu: zużycie i zniszczenie
Z biegiem czasu granulatory mogą zużywać się na swoich elementach, co wpływa na ich wydajność i trwałość[3]. Czynniki takie jak ścieralność surowców, niewłaściwa konserwacja lub długotrwałe użytkowanie mogą przyczynić się do zwiększonego zużycia krytycznych części maszyny.
Rozwiązanie
Aby rozwiązać problem zużycia, niezbędna jest regularna konserwacja i kontrola granulatora. Obejmuje to smarowanie ruchomych części, wymianę zużytych elementów, takich jak rolki i matryce, oraz zapewnienie prawidłowego ustawienia maszyny.
Używanie trwałych części wysokiej jakości, a także wdrażanie harmonogramów konserwacji zapobiegawczej może pomóc przedłużyć żywotność granulatora i utrzymać jego optymalną wydajność.
Wnioski
Podsumowując, obsługa granulatora w 2023 roku wiąże się z różnymi wyzwaniami, które mogą wpłynąć na wydajność i produktywność maszyny.
Rozwiązując typowe problemy omówione w tym artykule, takie jak niespójna jakość peletu, blokada matrycy, niskie tempo produkcji, emisja pyłu, wysokie zużycie energii, przeciążenie/zakleszczenie, nierówna twardość peletu, wibracje/hałas oraz zużycie, operatorzy mogą przezwyciężyć te przeszkody i zoptymalizować procesy produkcji pelletu.
Aby osiągnąć stałą jakość pelletu, operatorzy powinni skupić się na odpowiednim kondycjonowaniu materiału, konserwacji matrycy i optymalizacji sprzętu.
Wdrożenie skutecznych systemów odpylania i przestrzeganie protokołów bezpieczeństwa może pomóc ograniczyć emisję pyłu i zapewnić zdrowe środowisko pracy. Optymalizując zużycie energii i zapobiegając przeciążeniom lub zacięciom, operatorzy mogą zwiększyć wydajność i zrównoważony rozwój swoich operacji.
Co więcej, rozwiązanie problemów, takich jak nierówna twardość pelletu, wibracje i hałas, może poprawić ogólną wydajność i żywotność granulatora.
Dla operatorów poszukujących niezawodnych peletek i kompleksowych rozwiązań, TCPEL jest zaufaną firmą produkującą peletki B2B. Dzięki swoim najnowocześniejszym maszynom do peletowania i specjalistycznej wiedzy w branży, TCPEL oferuje niezawodny sprzęt i usługi, które pomogą operatorom sprostać wyzwaniom omówionym w tym artykule.
Aby dowiedzieć się więcej o peletkach firmy TCPEL i o tym, jak mogą usprawnić procesy produkcji peletu, odwiedź stronę stronie internetowej firmy TCPel. Zapoznaj się z ich ofertą maszyn do peletowania na stronie maszyny do peletowania TCPel lub dowiedz się o ich rozwiązaniach w zakresie maszyn do peletowania paszy na stronie maszyny do peletowania paszy TCPel.
Partnerstwo z TCPEL zapewnia dostęp do najnowocześniejszych technologii i wsparcia, umożliwiając operatorom optymalizację produkcja pelletu i odnieść sukces w branży.
Porozmawiaj z Ekspertem
PODZIEL SIĘ TYM POSTEM
Porozmawiaj z Ekspertem