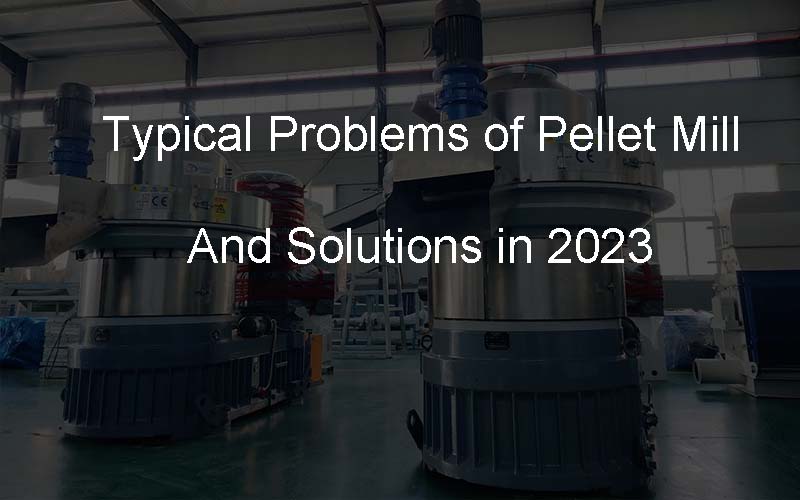
Гранулятор: типичные проблемы и решения в 2023 году
Существует ряд проблем при использовании грануляторов. Пользователи грануляторов сталкиваются с рядом типичных проблем, которые могут затруднить их производственные процессы.
Нестабильное качество пеллет, выбросы пыли, высокое потребление энергии и отказы оборудования — все это влияет на эффективность, производительность и общую прибыльность.
В этой статье мы рассмотрим наиболее распространенные проблемы, возникающие на грануляторах, и предложим практические решения для их устранения.
Приняв надлежащие методы технического обслуживания, оптимизируя рабочие параметры и реализуя эффективные стратегии, операторы могут преодолеть эти проблемы и увеличить производство окатышей.
Мы представим TCPEL, ведущую B2B гранулятор компании и ее решения, которые помогут пользователям преодолеть эти проблемы. Итак, давайте рассмотрим типичные проблемы грануляторов в 2023 году и найдем возможные решения их преодоления.
Как работает гранулятор
Прежде чем углубляться в конкретные проблемы грануляторов, важно понять принцип их работы.
Грануляторы могут превращать сырье в пеллеты. В том числе древесные пеллеты, пеллеты из биомассы. Эти гранулы можно использовать для различных целей. Например, топливо, корм для животных.
Сырье будет гранулироваться на грануляторах в цилиндрические гранулы. Происходит серия процессов: нагревание, увлажнение и обработка.
Пеллетные мельницы состоят из нескольких компонентов, включая питатель, кондиционер, пресс-форму для гранул, ролики и двигатель. Питатель обеспечивает равномерный поток сырья в машину, а кондиционер добавляет влагу и тепло для облегчения процесса гранулирования.
Матрица для гранул и ролики оказывают давление и сжатие на материалы, формируя из них гранулы желаемого размера и плотности. Двигатель обеспечивает необходимую мощность для работы машины[1].
Если вы хотите найти лучший способ решения проблем во время обработки, узнайте больше об основах работы гранулятора.
Имея глубокое понимание того, как работает машина и ее ключевые компоненты, операторы могут лучше устранять проблемы и внедрять эффективные решения.
В следующих разделах мы рассмотрим общие проблемы, с которыми столкнутся заводы по производству гранул в 2023 году, и предложим практические решения для их преодоления.
Заводы по производству комбикормов: нестабильное качество пеллет
Одной из распространенных проблем, возникающих при использовании гранулятора, является нестабильное качество гранул. Гранулы могут различаться по размеру, плотности и долговечности, что может повлиять на их производительность и рыночную стоимость.
Нестабильное качество пеллет может привести к неудовлетворенности клиентов и снижению прибыльности.
Решения
Чтобы решить эту проблему, крайне важно обеспечить надлежащую обработку и кондиционирование сырья перед подачей в камеру гранулирования.
Контроль содержания влаги, размера частиц и температуры материала может значительно улучшить качество гранул. Надлежащее кондиционирование помогает смягчить сырье, облегчая формирование гранул[2].
Кроме того, использование высококачественных матриц грануляторов, а также их регулярный осмотр и техническое обслуживание могут способствовать стабильному качеству гранул.
Заводы по производству древесных гранул: засорение матриц для гранул
Еще одной проблемой, с которой сталкиваются операторы грануляторов, является блокировка или засорение матрицы гранул. Это может произойти из-за таких факторов, как высокое содержание влаги, чрезмерное скопление материала или попадание посторонних предметов в головку.
Засорение матрицы нарушает процесс производства пеллет и требует частых остановок машины для очистки.
Решения
Чтобы предотвратить засорение, важно контролировать и поддерживать надлежащую влажность сырья. Чрезмерная влажность может привести к слипанию материала и закупорке матрицы[3].
Регулярный осмотр матрицы на наличие признаков засорения или повреждения и тщательная ее очистка помогут избежать сбоев в производстве.
Кроме того, внедрение надлежащих методов подачи, таких как использование равномерной и постоянной скорости подачи, а также использование подходящих добавок, может способствовать более плавной работе и снизить риск засорения матрицы.
Пресс-гранулятор: низкие темпы производства пеллет
Грануляторы часто сталкиваются с проблемами, связанными с низкой скоростью производства гранул. Такие факторы, как неэффективное сжатие, недостаточная толщина пресс-формы или изношенные детали, могут способствовать снижению производительности.
Низкие темпы производства могут препятствовать удовлетворению потребностей клиентов и ограничивать получение доходов.
Решения
Для увеличения производства гранул крайне важно оптимизировать процесс прессования, регулируя параметры гранулятора, такие как толщина пресс-формы, давление вальцов и температура кондиционирования.
Толщина матрицы должна соответствовать конкретному перерабатываемому сырью, чтобы обеспечить надлежащее сжатие и формирование гранул[4].
Регулярный осмотр и замена изношенных деталей, таких как ролики и матрицы, также важны для поддержания оптимальной производительности.
Кроме того, обеспечение правильной смазки и выравнивания гранулятора может способствовать повышению производительности.
Производители грануляторов: выбросы пыли
Выбросы пыли являются серьезной и широко распространенной проблемой, которую операторы должны решать при эксплуатации грануляторов. Наличие чрезмерного количества пыли в производственном помещении может создать ряд проблем с серьезными последствиями.
Во-первых, это представляет опасность для здоровья операторов, которые ежедневно подвергаются воздействию переносимых по воздуху частиц. Вдыхание пыли может привести к респираторным заболеваниям и другим осложнениям со здоровьем, что ставит под угрозу благополучие рабочей силы.
Накопление пыли может помешать правильной работе оборудования гранулятора. Когда пыль оседает на чувствительных компонентах, таких как двигатели, ремни и системы управления, это может привести к сбоям в работе, поломкам и незапланированным простоям.
Это не только нарушает производственный процесс, но также приводит к увеличению затрат на техническое обслуживание и снижению общей эффективности.
Чрезмерное количество пыли может негативно повлиять на рабочую среду, создавая дискомфорт для операторов. Запыленный воздух может уменьшить видимость, создать дискомфорт и повлиять на общую чистоту помещения.
Кроме того, если выбросы пыли не контролировать должным образом, это может привести к несоблюдению нормативных стандартов и экологических норм, что может привести к штрафам и санкциям.
Решения
Чтобы уменьшить выбросы пыли, необходимо внедрить эффективные системы сбора пыли, такие как циклоны или рукавные фильтры. Эти системы улавливают и удерживают пыль, образующуюся в процессе гранулирования.
Регулярная очистка и техническое обслуживание оборудования, в том числе гранулятора и связанных с ним систем вентиляции, может значительно снизить уровень запыленности. Надлежащее обращение с сырьем и его хранение также могут помочь свести к минимуму образование пыли.
Использование материалов с низким содержанием пыли или предварительно подготовленных материалов может еще больше снизить количество образующейся пыли. Важно обучить операторов надлежащим процедурам борьбы с пылью и обеспечить их соответствующими средствами индивидуальной защиты для обеспечения безопасных условий труда.
Производители грануляторов: потребление энергии
Некоторые грануляторы сталкиваются с проблемами, связанными с чрезмерным потреблением энергии. Это может привести к увеличению эксплуатационных расходов и снижению общей эффективности машины.
Высокое потребление энергии может вызвать перегрузку энергоснабжения, увеличить выбросы углерода и повлиять на устойчивость процесса производства пеллет.
Решения
Для решения проблемы высокого энергопотребления крайне важно оптимизировать рабочие параметры гранулятора. Регулирующие факторы, такие как скорость ролика, толщина штампа и подготовка материала, могут помочь повысить энергоэффективность.
Найдя правильный баланс между усилием сжатия и подводимой энергией, операторы могут максимизировать производство гранул при минимальном потреблении энергии. Регулярное техническое обслуживание, включая смазку и центровку машины, также важно для снижения потерь энергии.
Переход на более энергоэффективные компоненты и использование передовых систем управления может еще больше способствовать экономии энергии.
Машины для гранулирования: перегрузка мельницы для гранулирования
Распространенной проблемой, с которой сталкиваются операторы грануляторов, является перегрузка или заклинивание гранулятора, что может произойти из-за таких факторов, как посторонние предметы, неправильная подача материала или неисправность оборудования.
Перегрузка или заклинивание могут привести к простою, задержке производства и повреждению компонентов гранулятора.
Решения
Чтобы предотвратить перегрузку и заклинивание, важно применять надлежащие методы обработки и подачи материала. Операторы должны следить за тем, чтобы сырье не содержало загрязнителей, таких как камни, металлы или крупные частицы, которые могут вызвать закупорку.
Регулярная проверка системы кормления и оборудования, включая кормушку и кондиционер, необходима для своевременного выявления и устранения любых проблем. Реализация мер безопасности, таких как металлодетекторы или магнитные сепараторы, может помочь предотвратить попадание посторонних предметов в гранулятор.
Кроме того, операторы должны следовать инструкциям производителя по эксплуатации гранулятора в пределах его указанной производительности, чтобы избежать перегрузки.
Матрица гранулятора: Твердость гранул
Неравномерная твердость гранул является распространенной проблемой на грануляторах. Это относится к изменениям плотности и твердости производимых гранул. Непостоянная твердость может повлиять на качество пеллет и их характеристики при сжигании или кормлении животных.
Решения
Чтобы решить проблему неравномерной твердости гранул, важно обеспечить надлежащее кондиционирование и прессование сырья. Поддержание постоянного содержания влаги на протяжении всего процесса гранулирования имеет решающее значение для достижения равномерной твердости гранул.
Кроме того, регулировка давления ролика и толщины матрицы может помочь контролировать плотность и твердость гранул. Регулярная проверка и техническое обслуживание компонентов гранулятора, таких как ролики и матрицы, также важны для обеспечения стабильного качества гранул.
Машины для гранулирования: Шум гранулятора
На грануляторах обычно возникают проблемы с вибрацией и шумом, которые могут повлиять на рабочую среду и привести к повреждению оборудования.
Чрезмерная вибрация может привести к ускоренному износу машины, а высокий уровень шума может вызвать дискомфорт и повреждение слуха у операторов.
Решения
Чтобы смягчить проблемы с вибрацией и шумом, важно убедиться, что гранулятор правильно установлен и выровнен. Правильное выравнивание помогает свести к минимуму вибрацию и обеспечивает плавную работу.
Регулярный осмотр и техническое обслуживание компонентов машины, включая подшипники и ремни, также может снизить уровень вибрации.
Осуществление мер по звукоизоляции, таких как ограждение гранулятора или использование акустических барьеров, может помочь снизить уровень шума. Смазка движущихся частей, таких как подшипники, также может способствовать более плавной работе и снижению уровня шума[5].
Решая проблемы неравномерной твердости гранул и вибрации/шума, операторы могут повысить общую эффективность и производительность своих грануляторов, что приведет к улучшению качества гранул и улучшению условий труда.
Матрица гранулятора: засор из-за материалов с высоким содержанием клетчатки
При использовании материалов с высоким содержанием клетчатки, таких как некоторые виды сельскохозяйственных отходов или биомассы, грануляторы могут столкнуться с проблемами засорения матрицы. Высокое содержание клетчатки может привести к образованию стойких засоров в головке пеллет, что затруднит процесс производства пеллет.
Решения
Чтобы преодолеть закупорку матрицы, вызванную материалами с высоким содержанием клетчатки, важно внедрить эффективные методы подготовки материала. Предварительная обработка сырья, например, путем измельчения или измельчения, может помочь уменьшить длину волокна и облегчить производство гранул.
Кроме того, регулирование содержания влаги и использование подходящих связующих веществ или добавок может повысить текучесть материалов и предотвратить засорение матрицы. Регулярный осмотр и очистка головки гранул также имеют решающее значение для обеспечения бесперебойного производства гранул.
Машины-грануляторы: износ
Со временем компоненты грануляторов могут изнашиваться, что влияет на их производительность и срок службы[3]. Такие факторы, как абразивность сырья, неправильное техническое обслуживание или длительное использование, могут способствовать повышенному износу важных частей машины.
Решения
Для решения проблемы износа необходимо регулярное техническое обслуживание и осмотр гранулятора. Это включает в себя смазку движущихся частей, замену изношенных компонентов, таких как ролики и штампы, и обеспечение надлежащего выравнивания машины.
Использование высококачественных и долговечных деталей, а также соблюдение графиков профилактического обслуживания могут помочь продлить срок службы гранулятора и поддерживать его оптимальную производительность.
Заключение
В заключение, эксплуатация гранулятора в 2023 году сопряжена с различными проблемами, которые могут повлиять на эффективность и производительность машины.
Путем решения типичных проблем, обсуждаемых в этой статье, таких как непостоянное качество гранул, засорение матрицы, низкая производительность, выбросы пыли, высокое потребление энергии, перегрузка/заедание, неравномерная твердость гранул, вибрация/шум и износ, операторы могут преодолеть преодолеть эти препятствия и оптимизировать свои процессы производства пеллет.
Чтобы добиться стабильного качества гранул, операторы должны сосредоточиться на надлежащей подготовке материала, обслуживании матрицы и оптимизации оборудования.
Внедрение эффективных систем сбора пыли и соблюдение протоколов безопасности может помочь уменьшить выбросы пыли и обеспечить здоровую рабочую среду. Оптимизируя использование энергии и предотвращая перегрузку или заклинивание, операторы могут повысить эффективность и устойчивость своих операций.
Кроме того, решение таких проблем, как неравномерная твердость гранул, вибрация и шум, может улучшить общую производительность и долговечность гранулятора.
Для операторов, которым нужны надежные машины для производства пеллет и комплексные решения, TCPEL является надежной компанией по производству пеллет B2B. Благодаря своим современным пеллетным машинам и опыту работы в отрасли, TCPEL предлагает надежное оборудование и услуги, помогающие операторам преодолевать проблемы, обсуждаемые в этой статье.
Чтобы узнать больше об пеллетных машинах TCPEL и о том, как они могут улучшить процессы производства пеллет, посетите веб-сайт TCPel. Ознакомьтесь с их ассортиментом грануляторов на странице грануляторов TCPel или узнайте об их решениях для кормовых грануляторов на странице кормогрануляторов TCPel.
Партнерство с TCPEL обеспечивает доступ к передовым технологиям и поддержке, позволяя операторам оптимизировать свои производство пеллет и добиться успеха в отрасли.
Поговорите с экспертом
ПОДЕЛИТЬСЯ ЭТОЙ ЗАПИСЬЮ
Поговорите с экспертом